Au lendemain du Grand-Prix de Russie à Sotchi, nous sommes allés visiter l’usine d’Enstone, qui donne naissance aux Formule 1 de Renault. Après la reprise de Toleman (1981/1985), Benetton s’est installé au Centre Technique de Whiteways (1986/2001). Renault a racheté la structure italienne en 2000, avant de remporter le Championnat du Monde de Formule 1 en 2005 et 2006. Entre 2011 et 2015, l’équipe a été dénommée Lotus Renault GP (2011) et Lotus F1 Team (2012/2015) avant l’annonce du retour de Renault, en tant que constructeur à part entière fin 2015 sous l’étendard Renault Sport Formula One Team. L’équipe française déploie ses activités sportives sur deux sites : Enstone, dans l’Oxfordshire (Royaume-Uni) pour la partie châssis et Viry-Châtillon, sud de Paris (France) pour le groupe propulseur.
Vallée du sport automobile
Au début des années 1990, Enstone a accueilli sa première écurie de F1. À l’époque, toutes les équipes ont adopté une monocoque en fibre de carbone, une révolution améliorant la sécurité, mais nécessitant plus d’espace. Voilà pourquoi Benetton Formula s’y est installé dès 1992. Comme de nombreuses structures sont basées dans un triangle entre Birmingham, Londres et Bristol, la région est officieusement surnommée la “vallée du sport automobile”. Haas est la plus au nord (Banbury), non loin de Mercedes (Brackley) et de Racing Point Force India (Silverstone). À l’est, on retrouve Red Bull Racing (Milton Keynes) et McLaren au sud-ouest de Londres (Woking). À l’opposé, Williams est placée le plus à l’ouest (Grove) au sud d’Enstone.
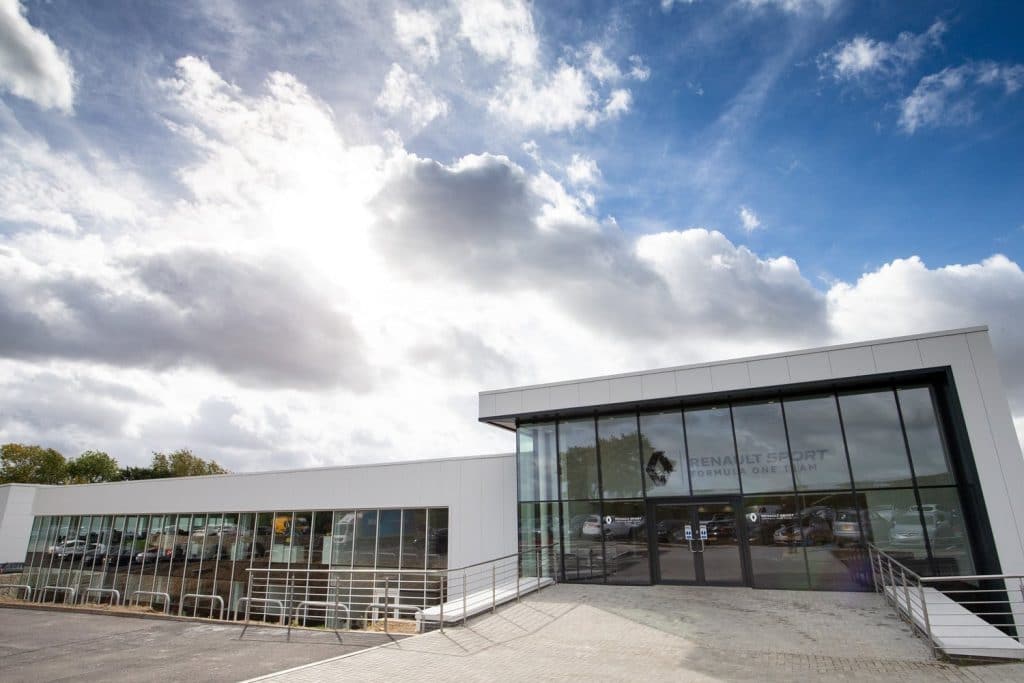
Enstone est le cœur de l’activité châssis (supervisée par l’ex FIA, Marcin Budkowski, Directeur Exécutif du site et “Nick” Chester Directeur Technique châssis). Mi-2018, 676 collaborateurs évoluent dans l’Oxfordshire, soit une croissance de 50% sur les trois dernières années et de 31% par rapport aux campagnes victorieuses de 2005 et 2006. 446 employés vivent dans un rayon de 25 miles autour de l’usine. Outre la conception du châssis et les unités de production, Enstone englobe le développement et l’intégration des boîtes de vitesses, l’électronique, la recherche et le développement, la soufflerie, un simulateur de pilotage, des bureaux d’ingénierie, un atelier de peinture et la base de l’équipe de course.
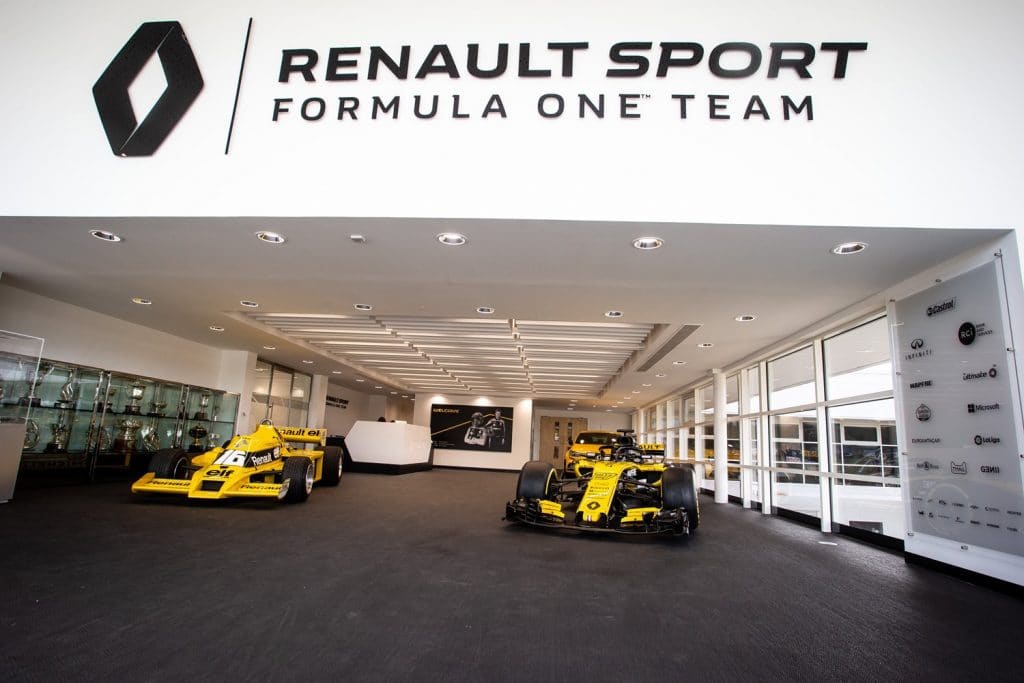
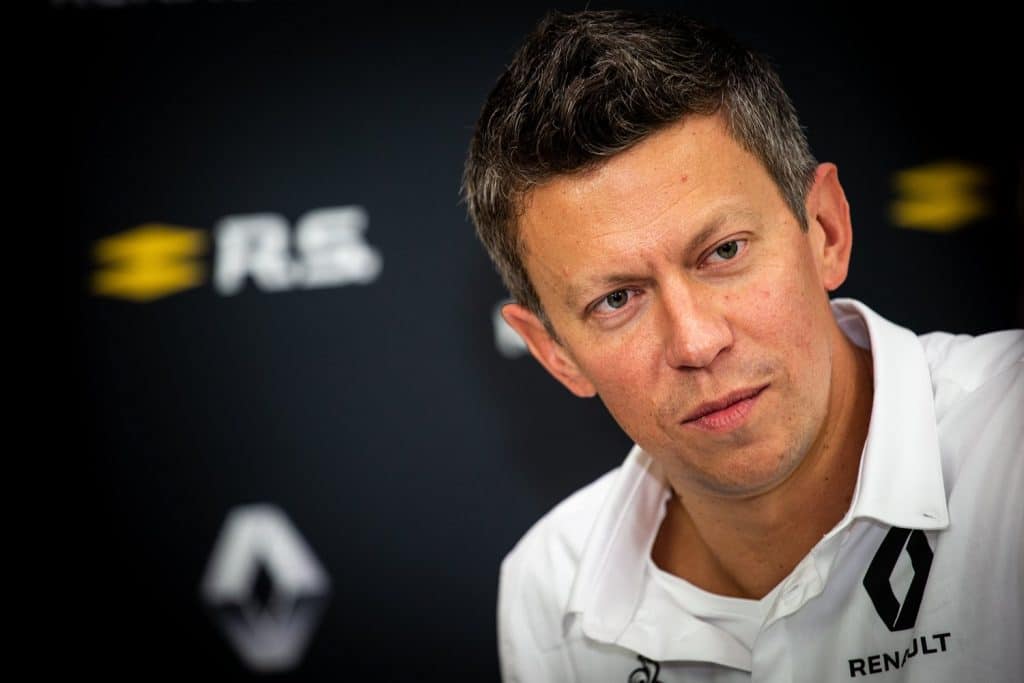
De l’autre côté de la Manche, Viry-Châtillon est le site dédié à la conception et au développement du groupe propulseur de Renault Sport Formula One Team et de ses équipes clientes. Situé au sud de Paris, Viry a une superficie deux fois moindre qu’Enstone avec 25 300 m2. Plus de 300 collaborateurs y évoluent pour concevoir, assembler et essayer le groupe propulseur employé en F1 (lire notre article ici) (sous la supervision de Rémi Taffin, directeur technique moteur). Viry abrite également la conception et la mise au point de la chaîne de traction utilisée en Formule E, ainsi que la base des compétitions clients organisées par Renault (Clio Cup, Formule Renault et Rallye).
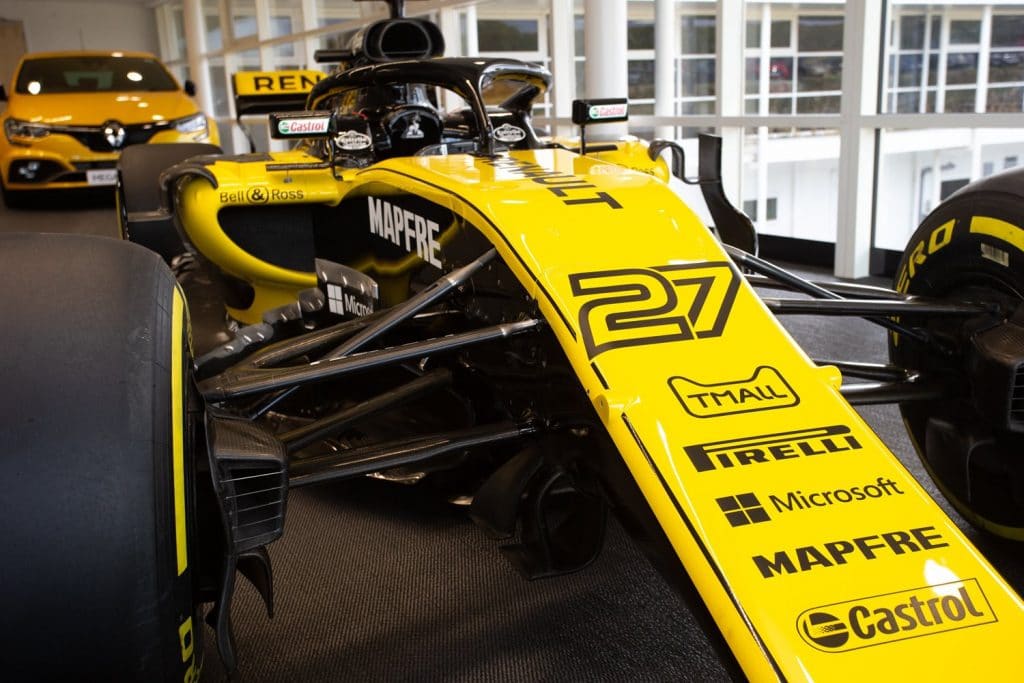
Viry-Châtillon est un lieu chargé d’histoire. Après avoir formé les locaux de Gordini dès 1969, la R.S.01, la première F1 engagée par Renault, y a vu le jour en 1977 (lire notre article ici). Depuis quatre décennies, le site a été grandement agrandi et amélioré afin de répondre aux défis technologiques de plus en plus grands du sport automobile. Plus récemment, un nouveau banc moteur a été installé cette année afin d’augmenter la précision et la finition du développement du groupe propulseur. En 2019, un bâtiment de 4 000 m2 sera finalisé pour accueillir les effectifs croissants et moderniser les installations actuelles. Enstone et Viry travaillent en étroite collaboration afin d’obtenir le meilleur ensemble châssis/groupe propulseur, dans le but d’assouvir ses ambitions en F1. Cette relation a déjà été couronnée de succès, et l’objectif de ces prochaines années est de récidiver comme lors des titres mondiaux acquis en 2005 et 2006 (lire notre article ici et là).
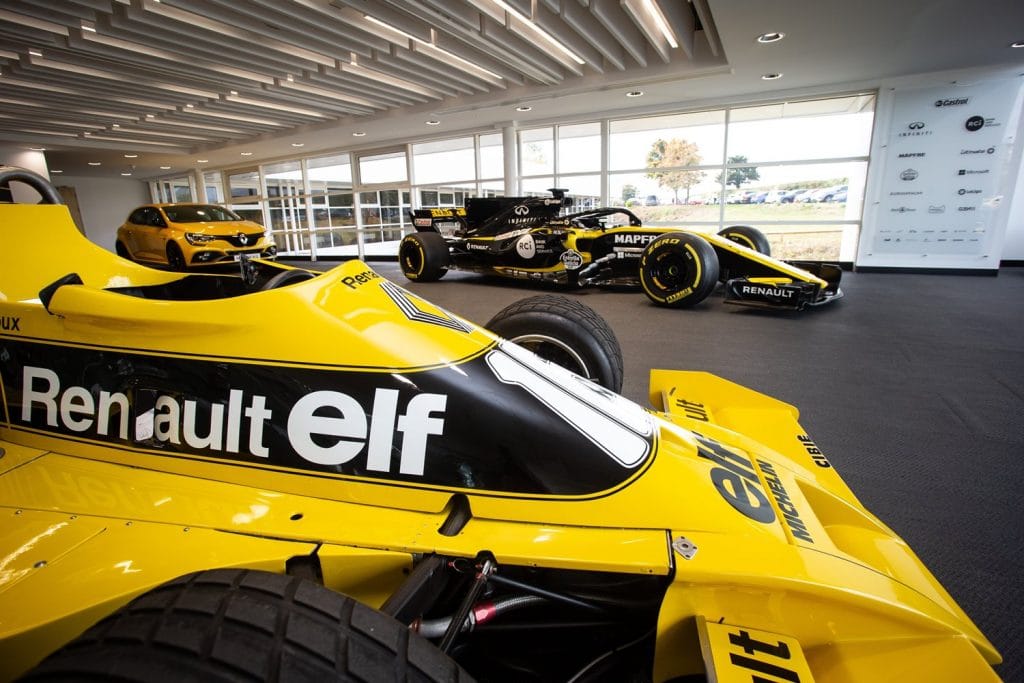
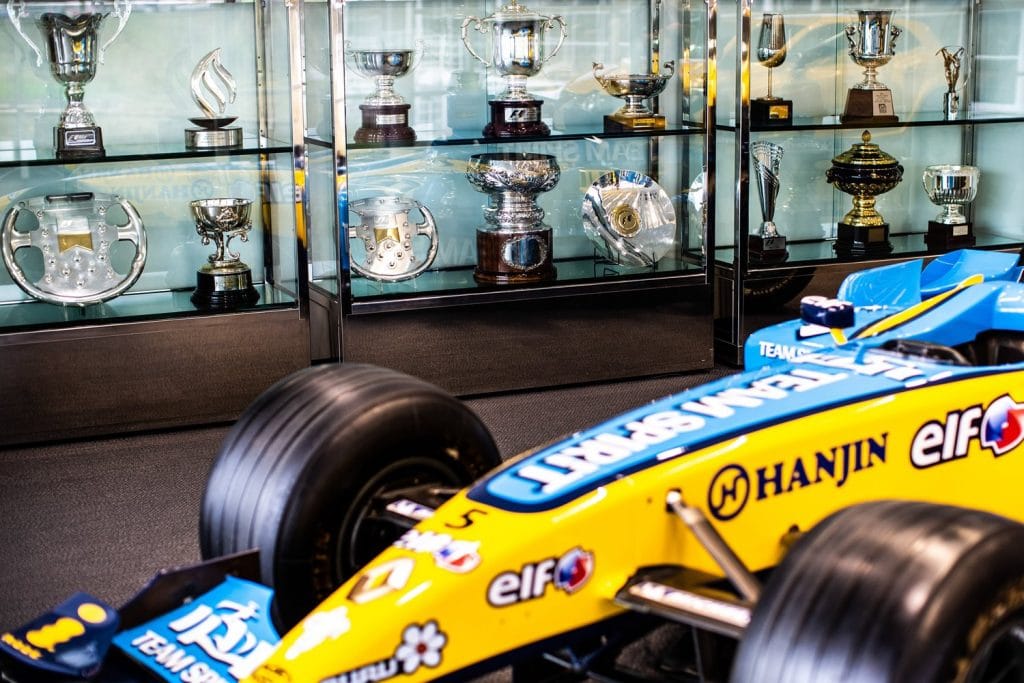
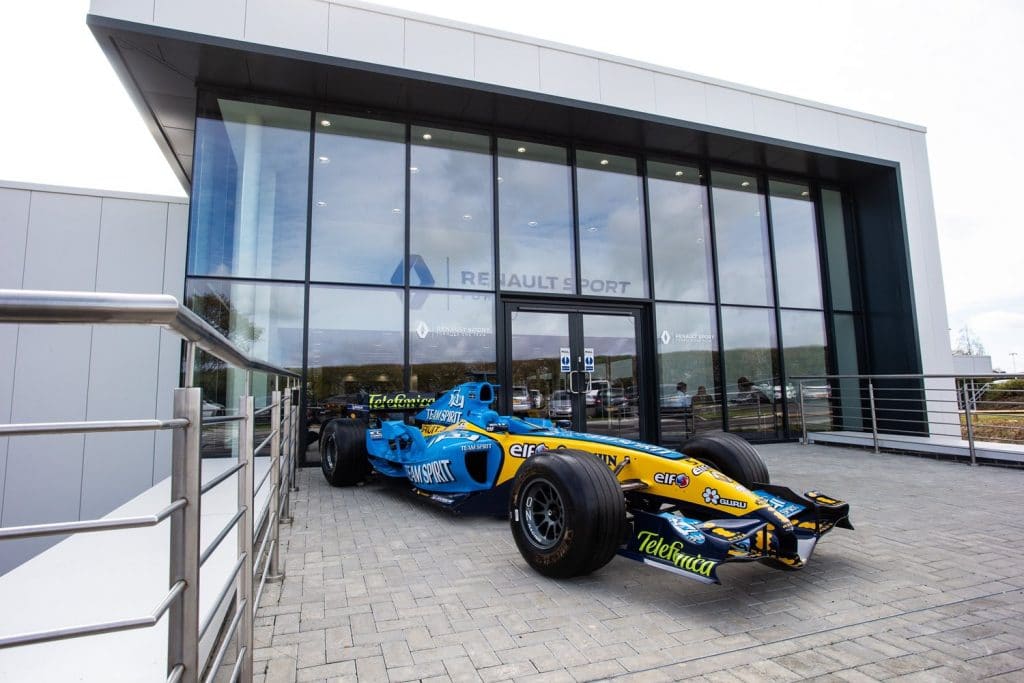
Conception : 150 000 h de travail, 19 000 dessins CAO, 14 500 pièces
La genèse d’une Formule 1 résulte d’un processus extrêmement complexe et détaillé durant lequel de nombreux facteurs sont à prendre en compte. Rien qu’à Enstone, plus de 70 collaborateurs participent au dessin du châssis dans le bureau d’études (BE). Le BE est divisé en différentes sections : conception de la
transmission, conception mécanique, analyse des contraintes et Groupe de Performance du Véhicule (GPV). Cette mission débute 18 mois avant le début de la saison et il faut près de 150 000 heures de travail et 19 000 dessins en conception assistée par ordinateur (CAO) pour définir les 14 500 composants d’une voiture.
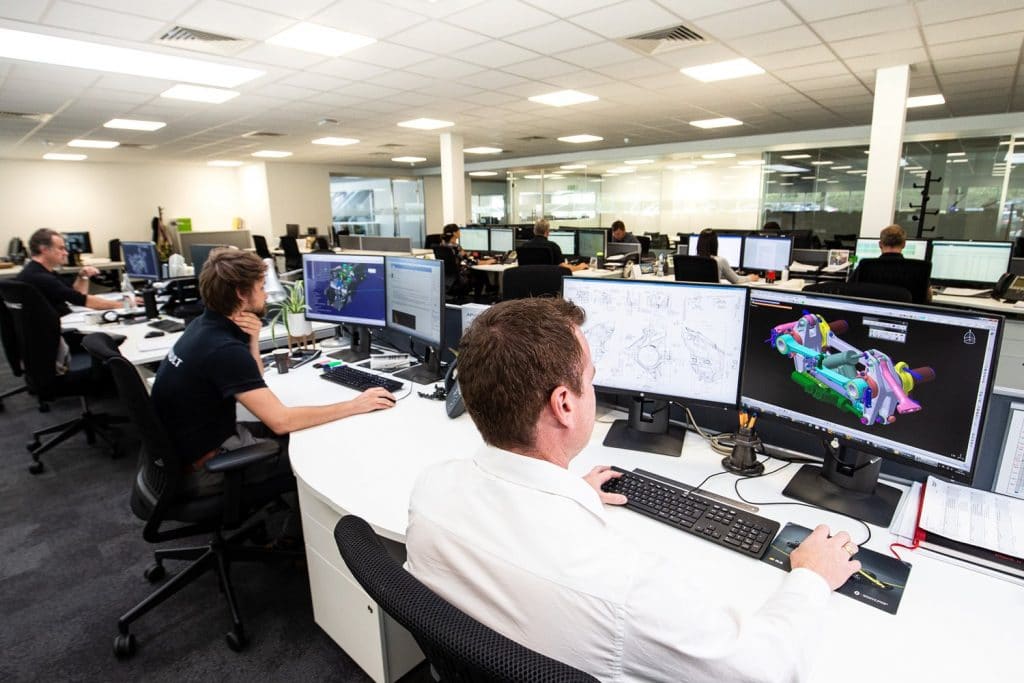
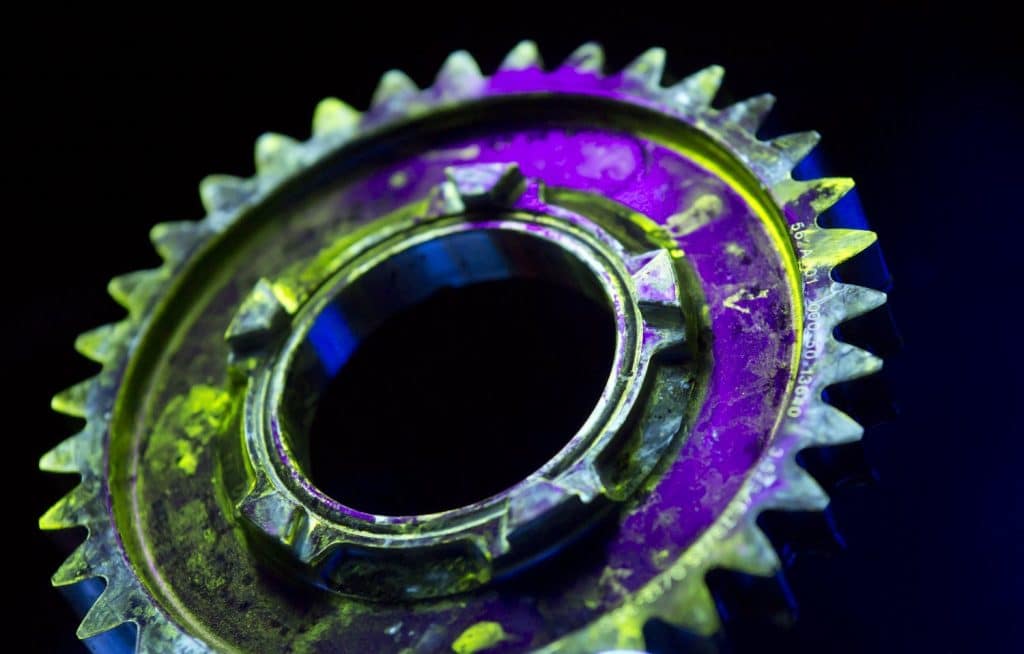
Un an avant le début d’une nouvelle campagne, la conception de la voiture est déjà bien avancée et les premiers composants sont mis à l’épreuve. Huit mois avant la première course, les séances de soufflerie s’intensifient. Les pièces sont ainsi testées, améliorées, le processus se poursuivant jusqu’aux premiers essais de pré-saison et tout au long de l’année. Le premier châssis est généralement prêt juste après Noël. Dès qu’une saison démarre, les plans et les dessins de la suivante commencent à Enstone afin de devancer la concurrence. Le juste équilibre reste difficile à atteindre, la performance en piste étant tout aussi importante que les préparatifs de l’année suivante. Si la conception de certains composants ne prend que quelques jours, d’autres, plus complexes, peuvent nécessiter plusieurs mois, comme la boîte de vitesses.
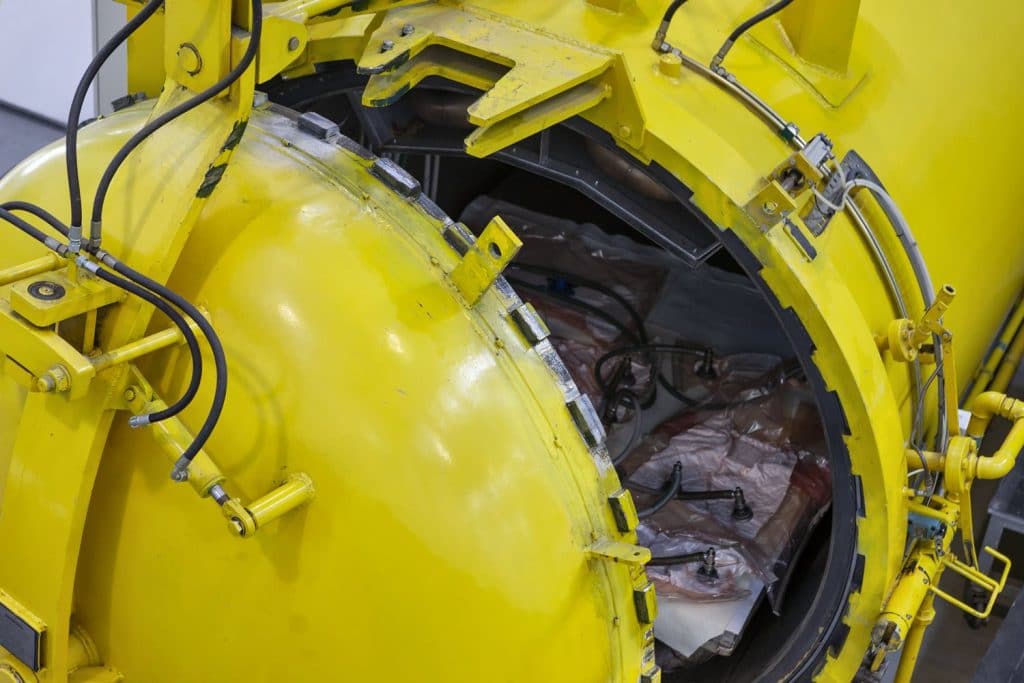
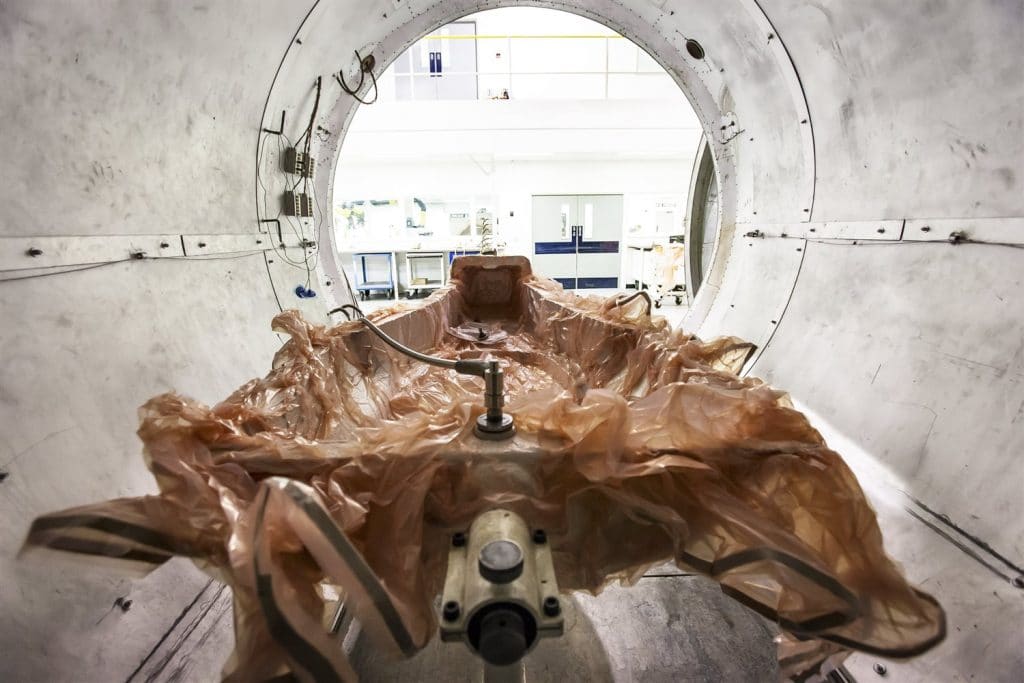
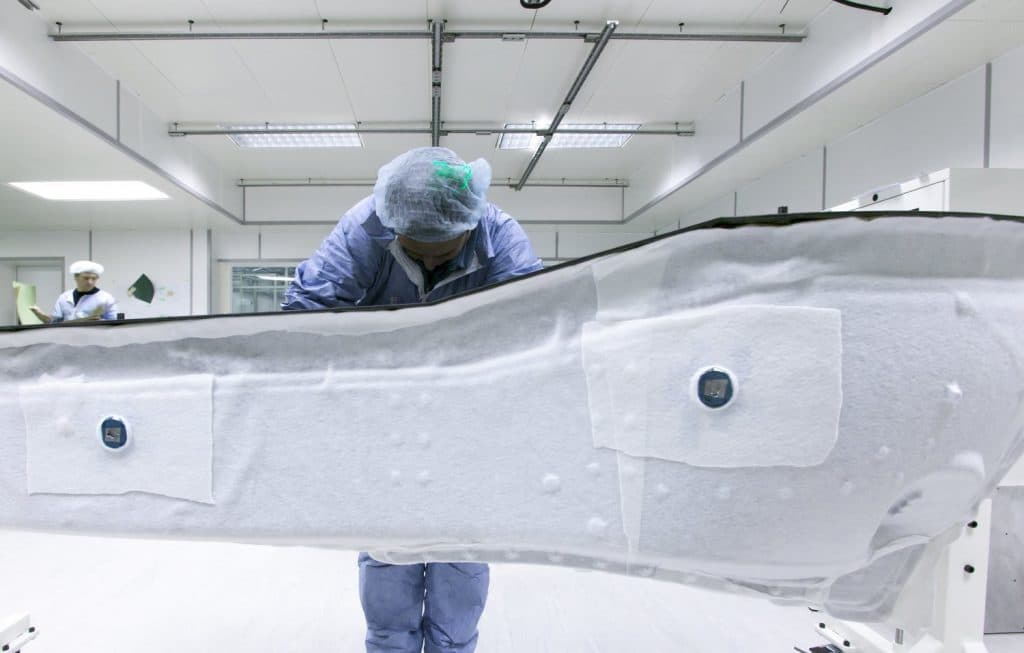
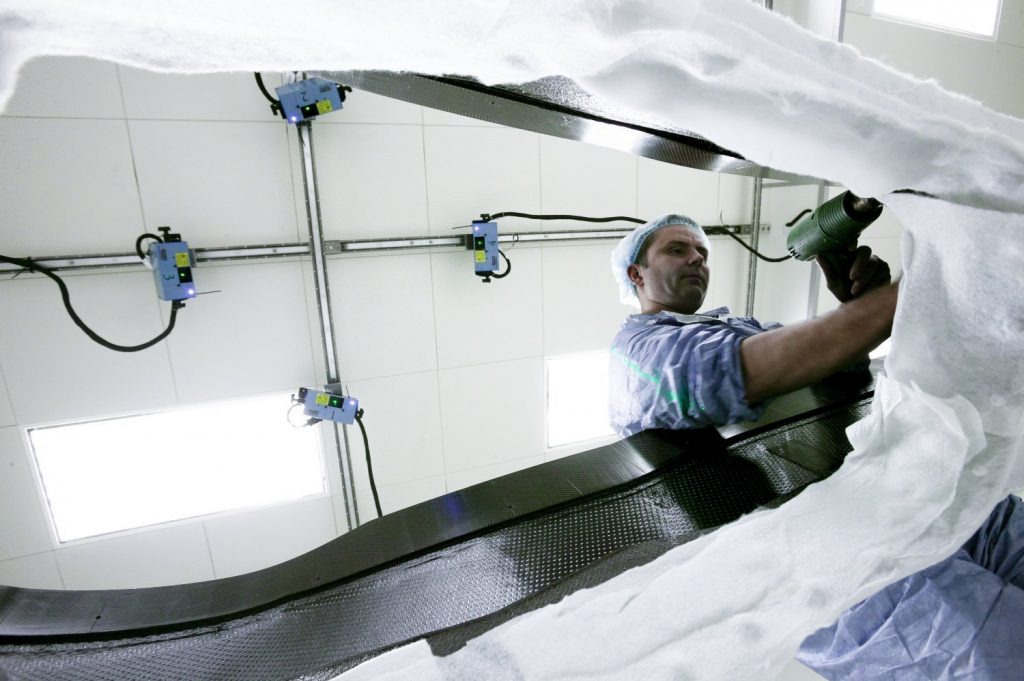
Soufflerie CFD : 520 passages en 8 semaines, 60 To de données par semaines
La Formule 1 est une discipline où l’aérodynamique tient une place très importante et cela se traduit dans la taille de ce département à Enstone. La soufflerie joue un rôle essentiel dans la conception, le développement et la compréhension aérodynamique d’une F1. D’une superficie de 2 674 m2, celle d’Enstone a été mise en service en 1998. Depuis 2014, la FIA encadre son utilisation pour limiter les coûts en vérifiant et en enregistrant l’historique de chaque équipe. Les écuries ne peuvent donc réaliser que 520 passages sur une période de 8 semaines définie ou 65 passages par semaine. Une maquette à 60% est placée sur une “piste roulante” face à un flux d’air fixé et restreint par la FIA à 50 mètres par seconde. Tous les éléments pouvant affecter la monoplace sont essayés en soufflerie, qui peut tester le tangage, le roulis, la hauteur de roulement, les appuis, la déformation des pneus et le système d’échappement afin d’examiner leur comportement et leur potentiel.
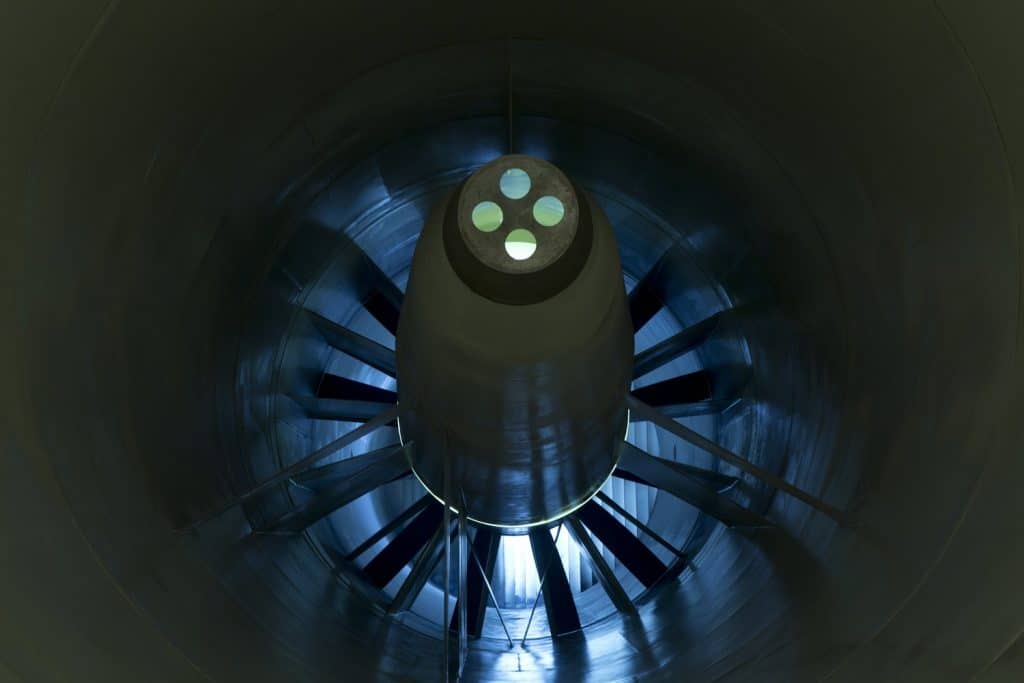
En 2017, la soufflerie d’Enstone a bénéficié d’une importante remise à niveau pour améliorer ladite piste et augmenter l’angle et la portée de lacet. La mécanique des fluides numériques (CFD) aide et révolutionne de manière significative ce processus de conception. Pour faire simple, il s’agit d’une soufflerie virtuelle où des superordinateurs dotés de logiciels de pointe permettent aux ingénieurs de simuler la complexité des flux à l’extérieur et à l’intérieur de la voiture à travers plus de 60 To de données par semaine. Situé sous terre, le centre CFD d’Enstone est pleinement opérationnel depuis 2008.
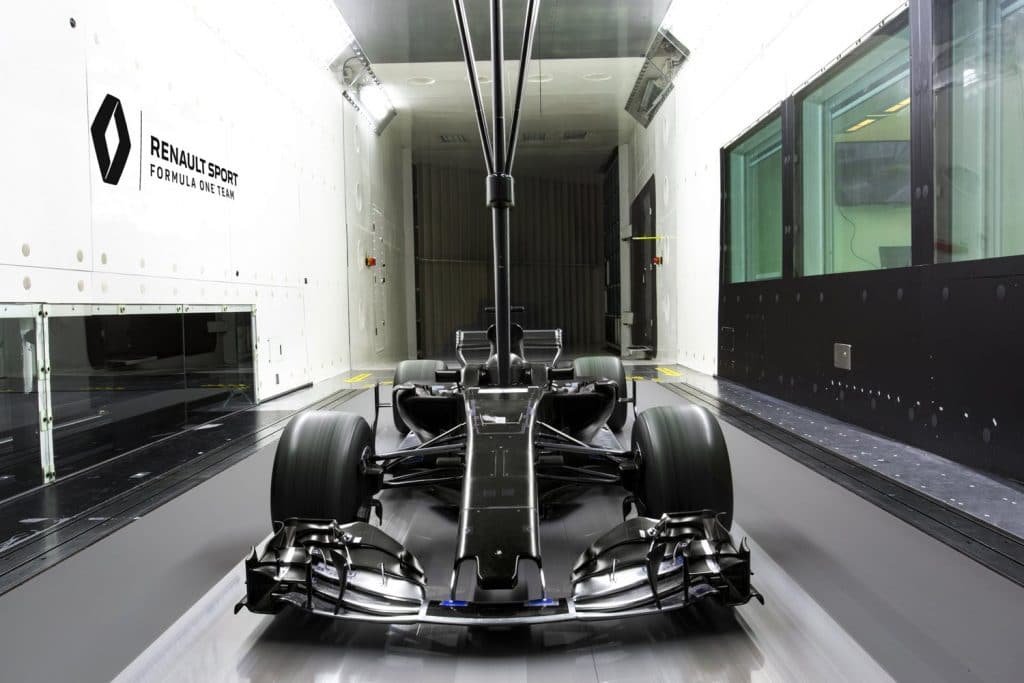
Fabrication : 90% du châssis produit en interne, 18 km de fibre de carbone et 50 000 pièces métalliques par saison
Plus de 90% du châssis est fabriqué en interne à Enstone, permettant un contrôle important sur la majeure partie de la production des pièces et garantissant un niveau de qualité requis. Le département de fabrication est chargé de réaliser les radiateurs, les échappements et d’autres petites pièces. Malgré les exigences d’une précision minutieuse, il n’y a pas meilleur moyen que d’y procéder manuellement. Le système d’échappement est tout particulièrement soigné avec une épaisseur variant de 1,1 à 0,3 mm à sa sortie. Si une part importante est faite à la main, le reste se compose de titane imprimé en 3D. Les échappements sont conçus à partir de feuilles extrêmement fines d’Inconel (développé par Rolls-Royce pour ses moteurs à réaction), un alliage à haute teneur en nickel résistant à des températures élevées, dans des environnements extrêmes où elles peuvent dépasser 1000°C, comme en Formule 1. Deux journées et demie sont nécessaires à deux personnes pour en fabriquer la majeure partie.
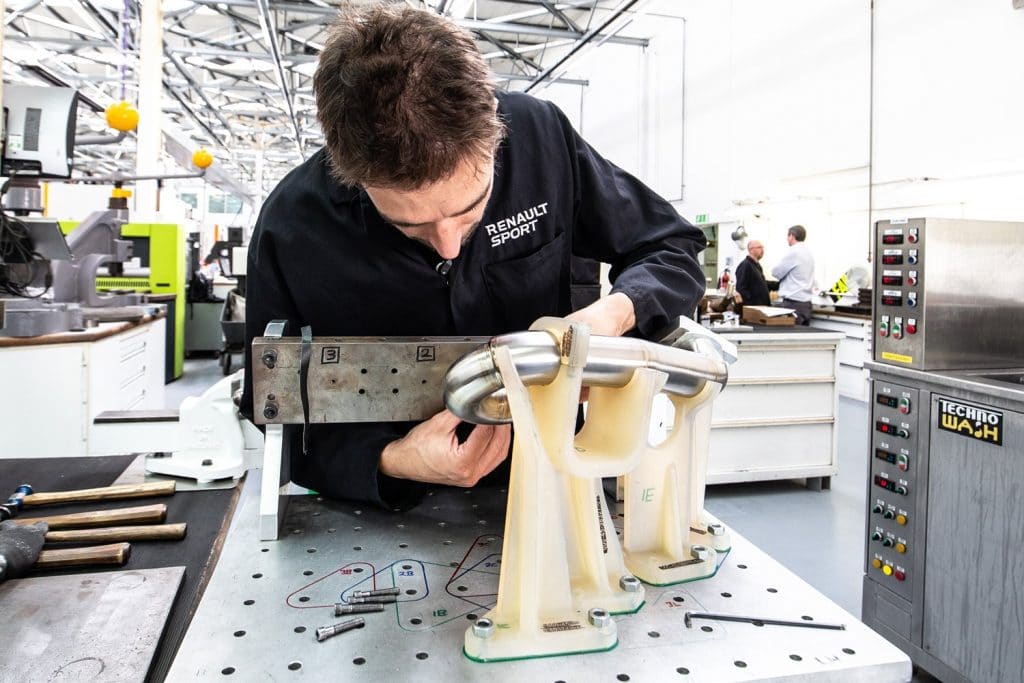
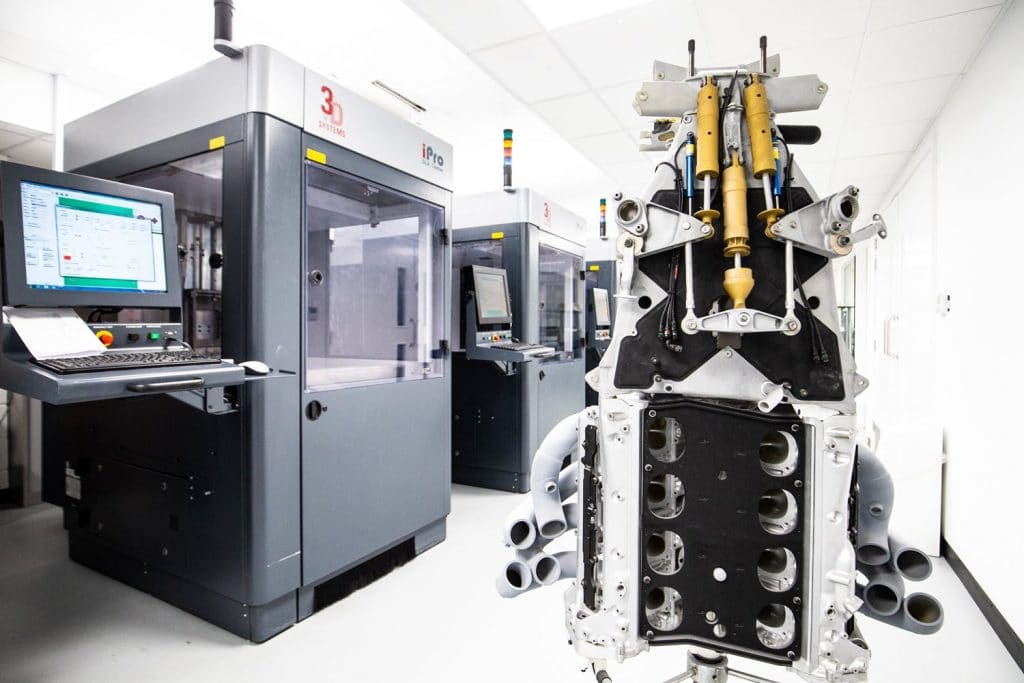
Les Composites forment l’un des plus grands départements d’Enstone, avec plus de 50 collaborateurs dédiés à la réalisation des patrons, découpes et montages. Conformément au règlement de la FIA, le poids minimum d’une F1 est aujourd’hui de 734 kg. L’objectif est donc de rendre la monoplace la plus légère possible, tout en tenant compte de la sécurité du pilote et des nombreux crash-tests auxquels il faut se soumettre. Du lest peut également être ajouté pour atteindre ce seuil légal (optimisation du centre de gravité de la voiture). L’équipe utilise massivement la fibre de carbone (2 fois plus résistant et 5 fois moins lourd que l’acier), dont la quantité employée équivaut à une bande de 18 km sur un mètre, qui a grandement contribué aux progrès de la sécurité en F1, au cours des vingt dernières années.
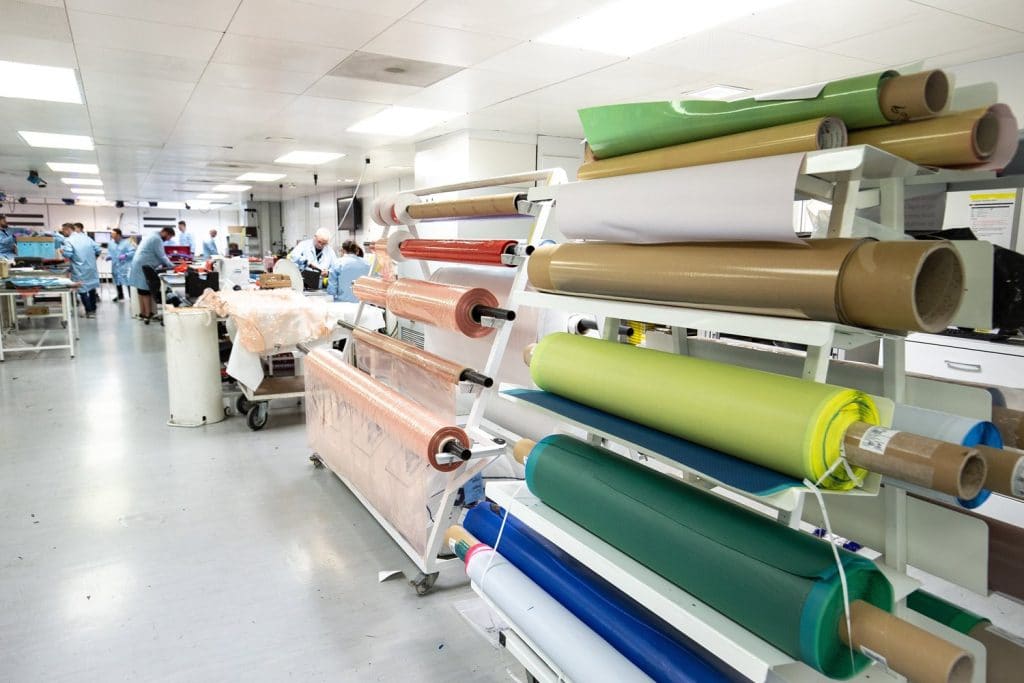
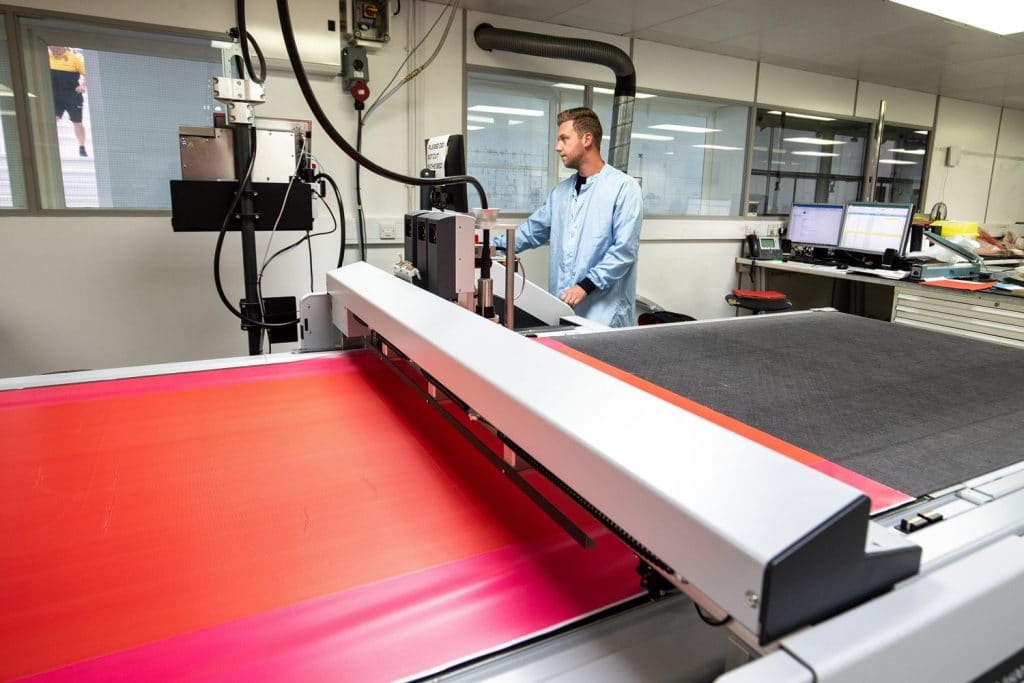
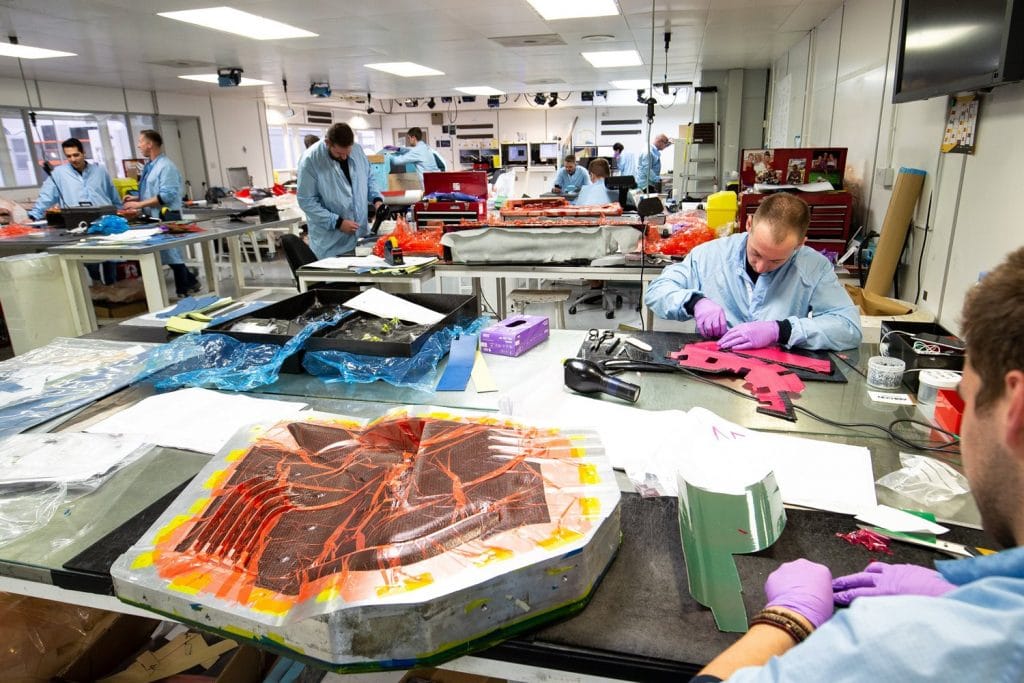
Enstone dispose d’un atelier ultramoderne où les pièces sont fabriquées à partir de métaux légers et résistants tels que le titane, l’aluminium et l’Inconel. Les technologies d’usinage les plus avancées sont utilisées afin de produire plus de 50 000 éléments métalliques sur une saison. Les outillages fonctionnent 24 heures sur 24 tout au long de l’année. 20 machines (90% d’entre elles ont été renouvelées l’an passé) type Commandes Numériques multi-axes. En 2017, deux nouvelles machines d’usinages verticaux, haute vitesse à 5 axes de très grande précision (Breton), y ont été installées, afin d’améliorer les châssis. Leur principale utilisation a trait à l’usinage des grandes pièces, comme les coques ou les fonds plats. La fabrication d’un châssis peut prendre jusqu’à cinq semaines de travail, mais la précision de ces machines permet de gagner 30% de temps par rapport aux précédentes.
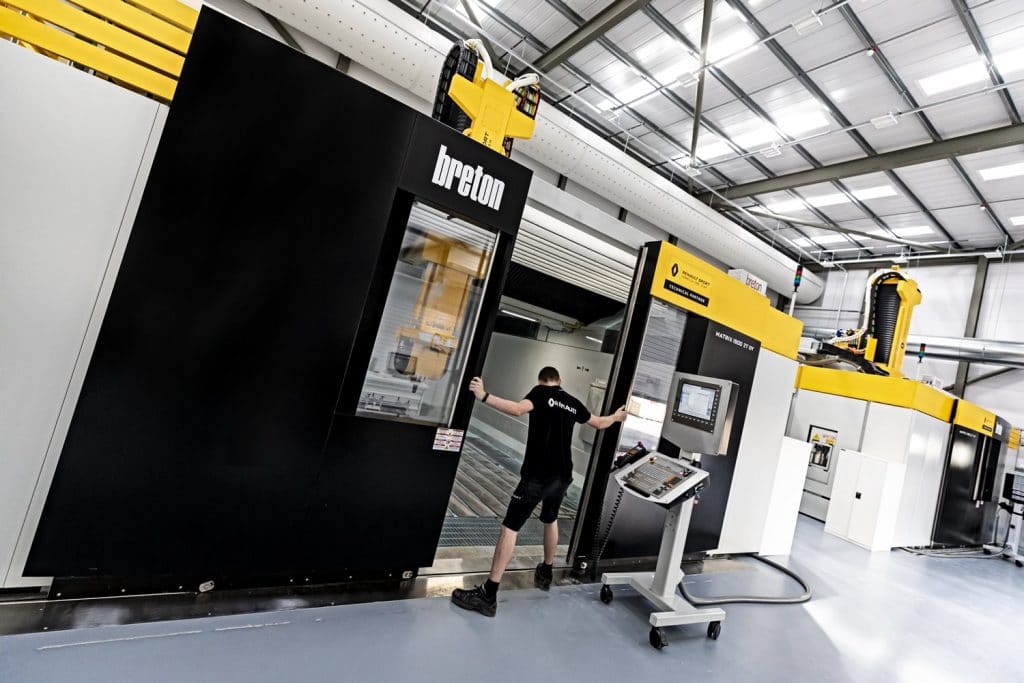
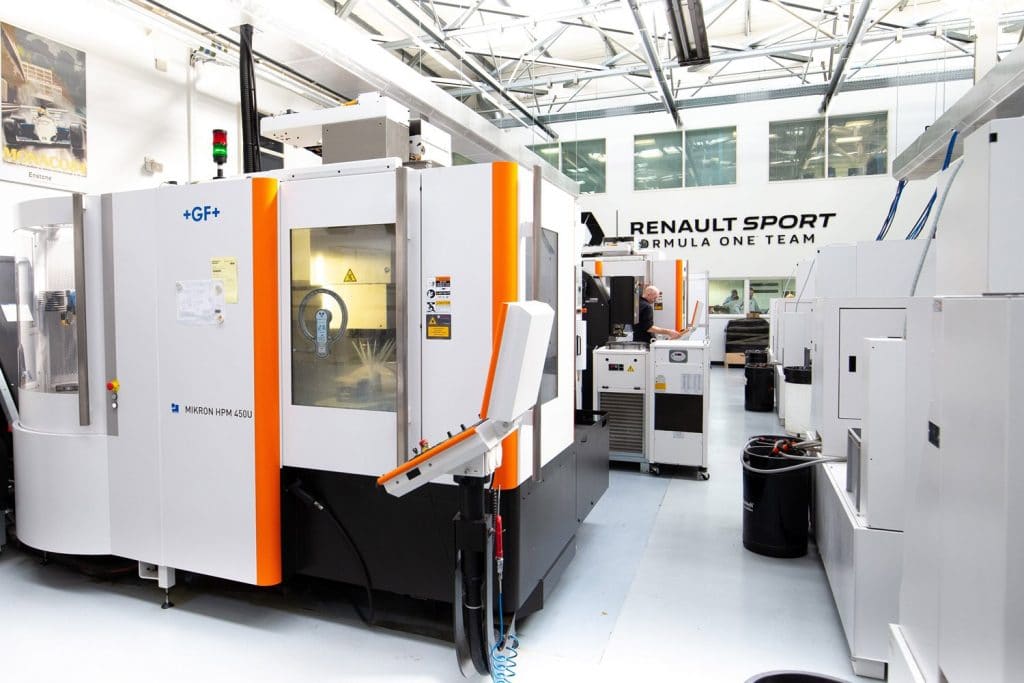
Le banc d’essais à sept vérins (élément clé de la R&D) permet d’améliorer les performances de la voiture à travers la suspension, en reproduisant le comportement de la monoplace sur le circuit testé au choix, dans l’environnement intégralement maîtrisé du laboratoire. Les données de l’équipe de piste, après les essais libres du vendredi, sont reçues et sont appliquées sur le banc, avec toutes les contraintes qui existent, pour définir un tour en référence, estimer l’impact des différents réglages, anticiper de nouveaux concepts tant pour la voiture actuelle que pour les futures.
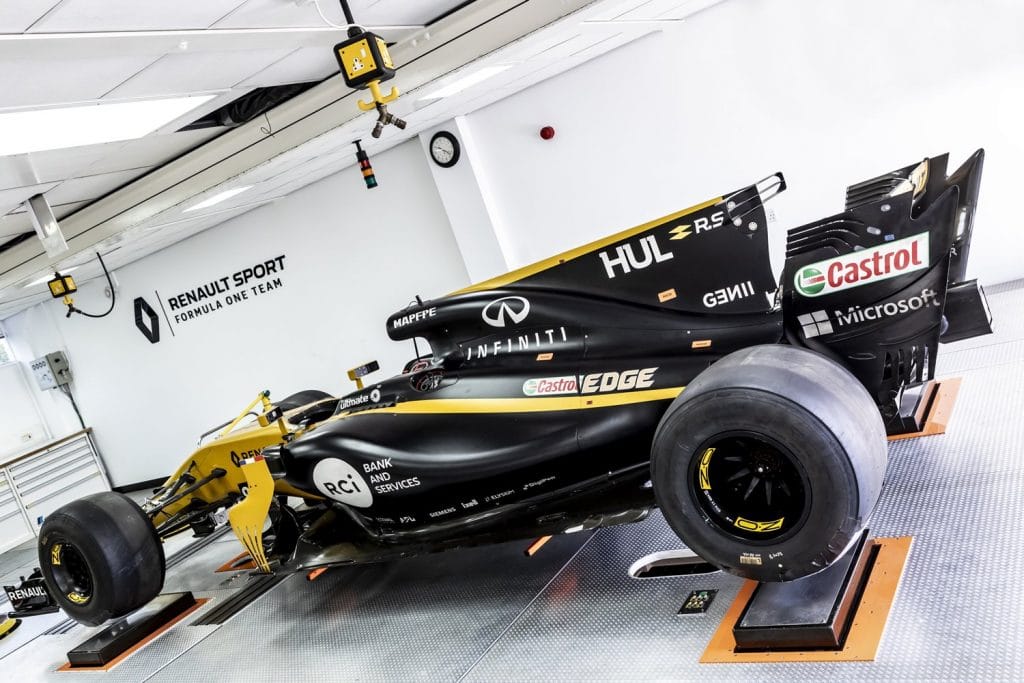
Electronique du volant estimée entre 35 000 et 45 000 €
Le volant des F1 du Renault Sport Formula One Team possède une valeur mécanique et électronique estimée entre 35 000 et 45 000 €. C’est un élément crucial en F1, étant donné sa capacité à contrôler la monoplace avec le moindre bouton. On en compte d’ailleurs une vingtaine, auxquels s’ajoutent différents interrupteurs ainsi qu’un écran LCD, adapté aux préférences des pilotes pour afficher des informations comme les temps au tour et les messages obligatoires de la FIA. Les pilotes peuvent choisir parmi plus de cent combinaisons pour extraire le maximum de leur voiture, en ajustant ainsi les réglages du différentiel pour l’entrée en virage, le déploiement de l’ERS, la gestion de l’énergie ou encore l’équilibre des freins, via 200 capteurs fournissant 150 000 mesures/sec, soit 4 Mo de données à la seconde ! Ceux ci sont développés et produits à Enstone grâce aux 20 personnes du département électronique : 8 ingénieurs, 7 concepteurs, 4 membres de l’équipe de course et 2 dans celle dédiée aux essais. Ils sont aussi responsables de la conception du volant, des communications radio entre le pilote, le garage et le muret des stands, et des systèmes de contrôle des arrêts et de la télémétrie.
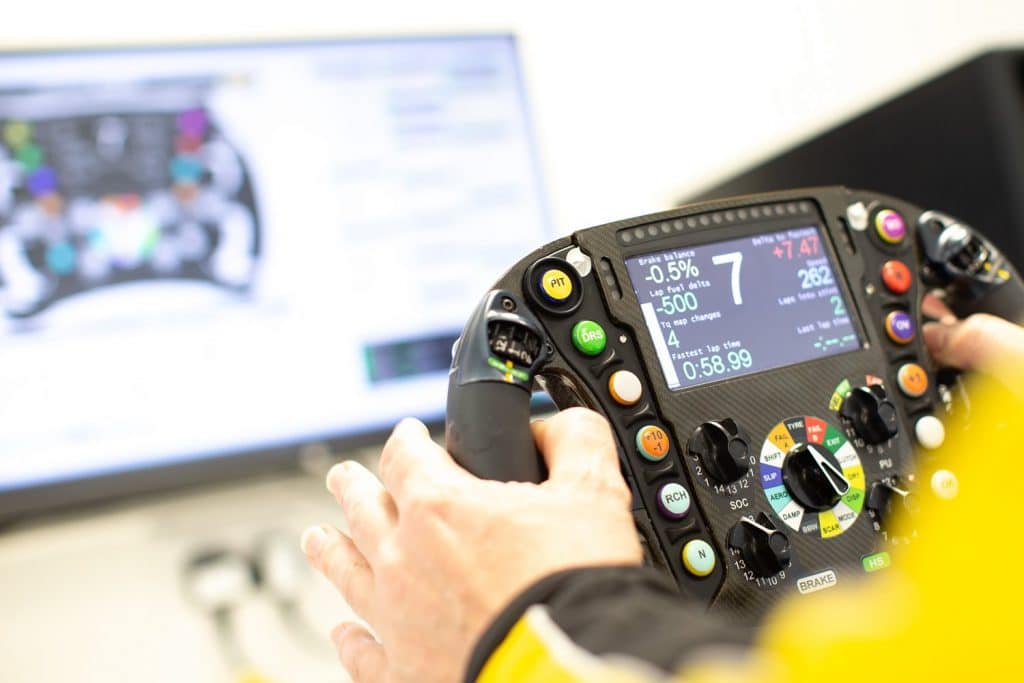
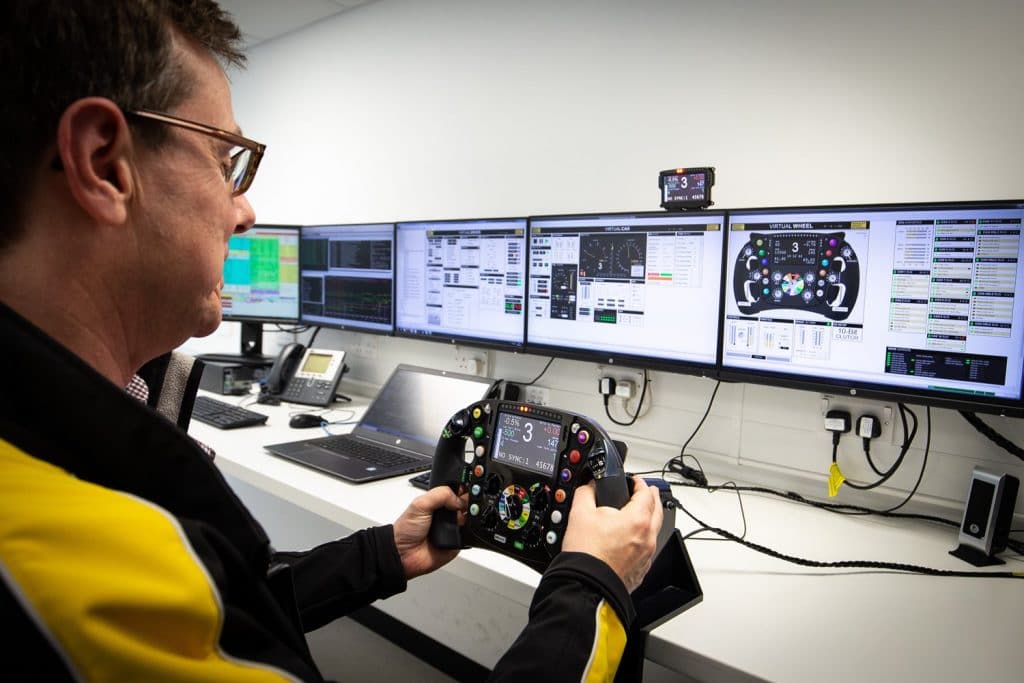
De même, la boîte de vitesses s’avère extrêmement complexe, avec huit rapports, plus la marche arrière. Son enveloppe est faite en fibre de carbone et conçue en interne à Enstone. Un système « Quickshift » extrêmement rapide permet d’optimiser chaque passage de vitesse. La monoplace vue aux essais de pré-saison et celle du dernier Grand Prix de la saison seront assez différentes.
33 000 kWh par an pour alimenter le simulateur
Le simulateur joue un rôle crucial dans le développement. Utile aux pilotes, ingénieurs, designers et au Groupe de Performance du Véhicule (GPV), celui d’Enstone a été mis en service en 2011. Il dispose d’un modèle de la voiture conçu par l’équipe et des tracés (fournis par le spécialiste de la simulation de conduite, R Factor Pro). Doté de cinq projecteurs haute définition, son système de direction offre une représentation et des sensations fidèles, notamment par rapport aux forces générées sur les pneus. La télémétrie est aussi précise que celle sur place et s’avère extrêmement importante dans la préparation d’un week-end. Les trois quarts de l’énergie consommée par le simulateur viennent de panneaux solaires pouvant produire 33 000 kWh/an. Contrairement aux simulateurs aéronautiques, celui d’Enstone ne permet pas de reproduire les 6G subis par la monoplace. Pour la compression du raidillon de Spa Francorchamps, il faudrait disposer d’une amplitude de 10 mètres soit 4 étages. Impossible dans l’état actuel bâtiment. Pour la simulation d’un tour de Sotchi 2018, le temps était de 1 min 48 sec, alors qu’en course le meilleur temps au tour a été réalisé en 1 min 35,861 sec. Le but est avant tout de tester les nouvelles pièces sur la monoplace, pas de battre le record du tour de chaque circuit.
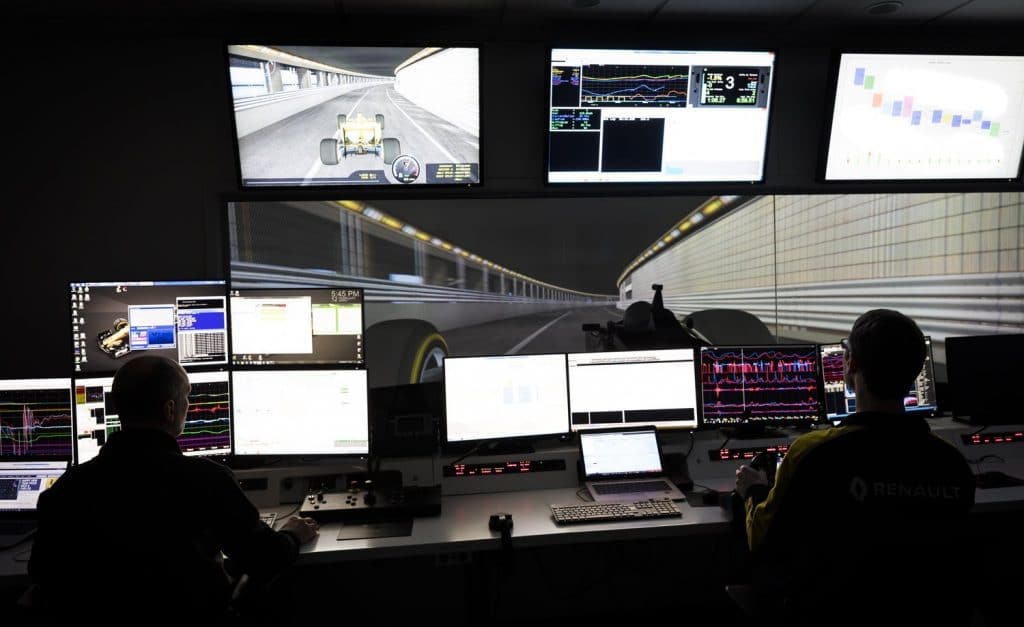
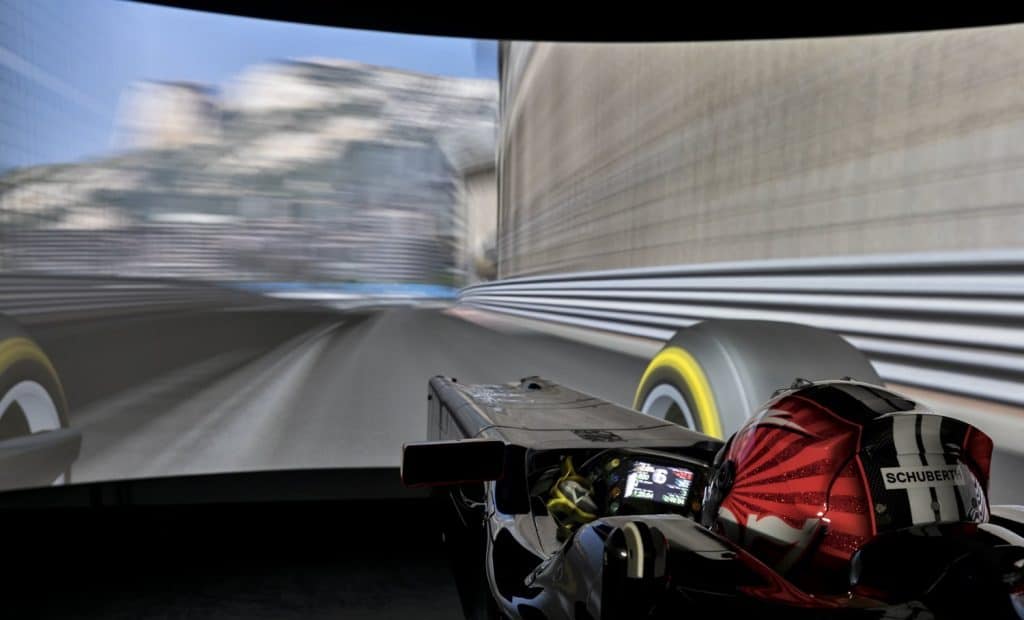
8 heures pour assembler une monoplace et 60 minutes pour changer la moteur
Les espaces de révision sont de véritables salles d’opération pour les monoplaces. Selon le lieu et la nature de la prochaine course, la voiture est démontée et les pièces sont inspectées, entretenues, voire remplacées. Les contrôles non destructifs et l’inspection permettent de s’assurer que le moindre élément est dans l’état prévu à tel instant de son cycle de vie. Après les manches européennes, les F1 retrouvent ces espaces le lundi ou le mardi à Enstone. Dès le jeudi soir, elles sont prêtes à repartir pour l’épreuve suivante. Suivant le calendrier, ce processus s’adapte lorsque la course se déroule sur un autre continent ou que deux Grands Prix s’enchaînent en une semaine. Dans ce cas, l’équipe de course prend le relais et peut désassembler et ré-assembler une monoplace en 8 heures et changer le moteur en 60 minutes.
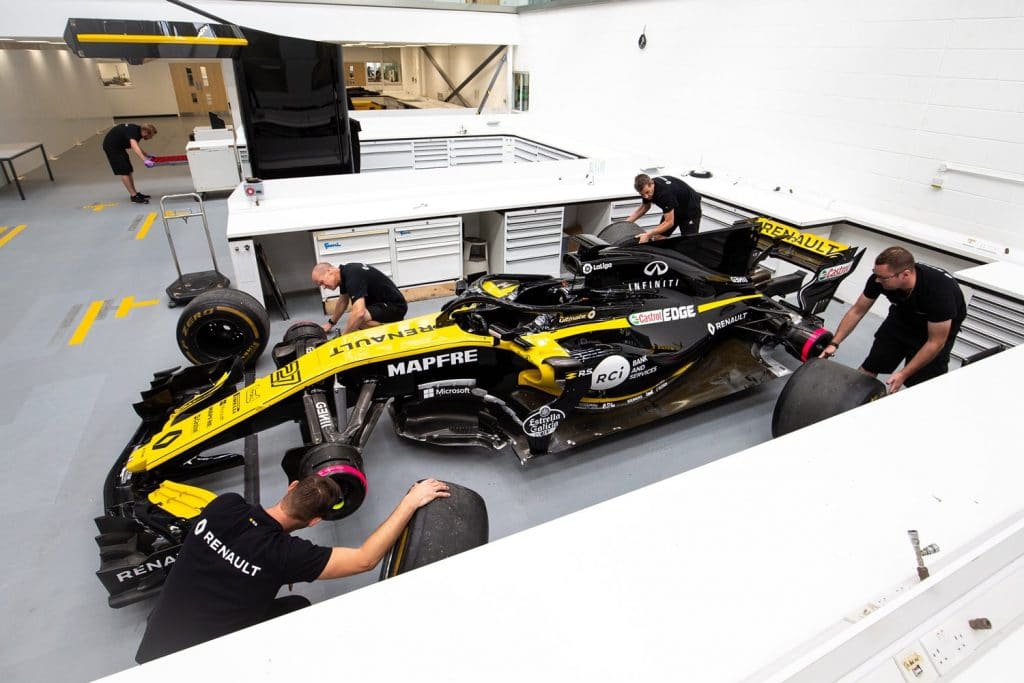
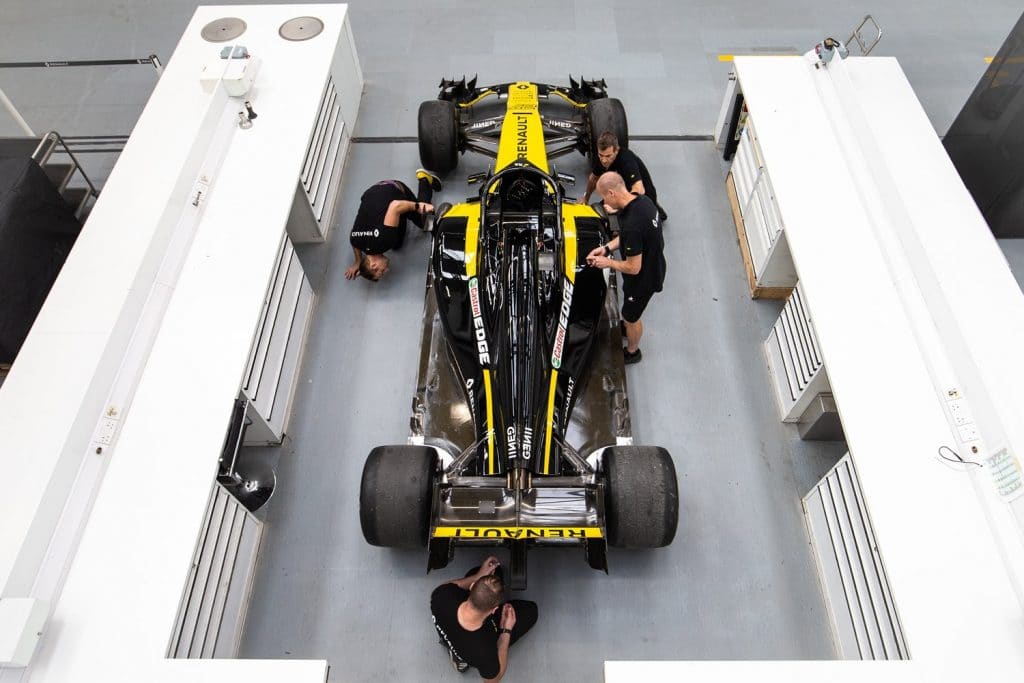
A chaque GP, le transport s’effectue via 16 semi-remorques, par le fret aérien (36 Tonnes) et maritime (3 conteneurs). En moyenne, plus de 500 éléments reviennent du circuit pour être entretenus, réparés, inspectés ou modifiés avant d’être réexpédiés sur la prochaine épreuve. Pour chacun des Grands-Prix, entre 70 et 90 membres de l’équipe font le déplacement. Conformément aux règles de la FIA, seulement 60 ont accès à la voiture, les autres venant de plusieurs départements, tels le marketing, la communication, les acquisitions et la restauration. Au cours d’une saison, 4 châssis sont fabriqués et l’écurie parcourt environ 160 000 km.
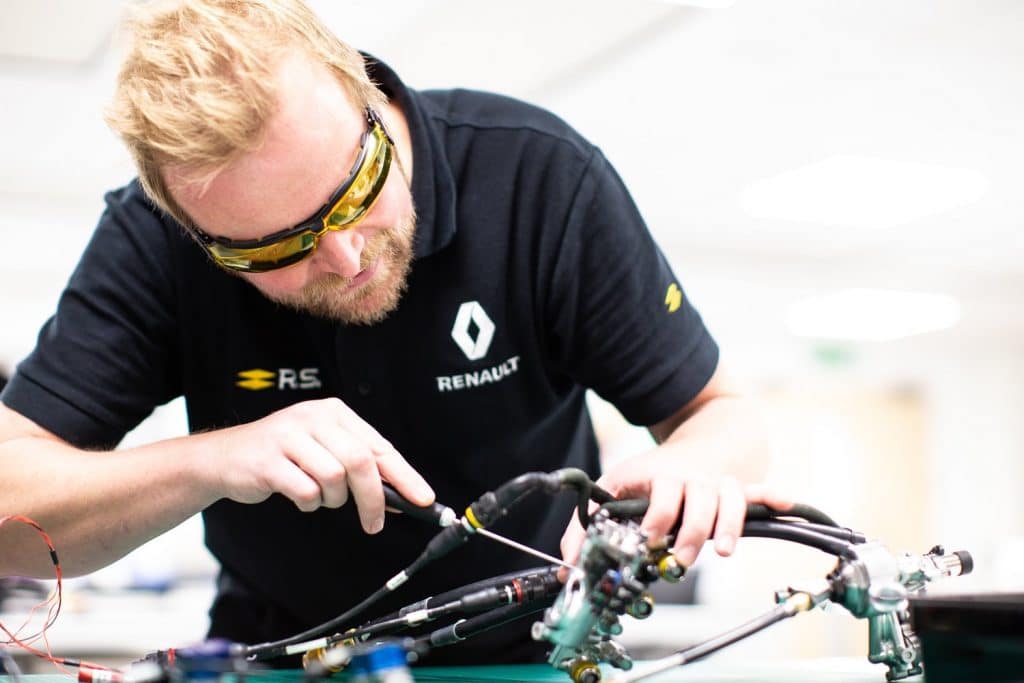
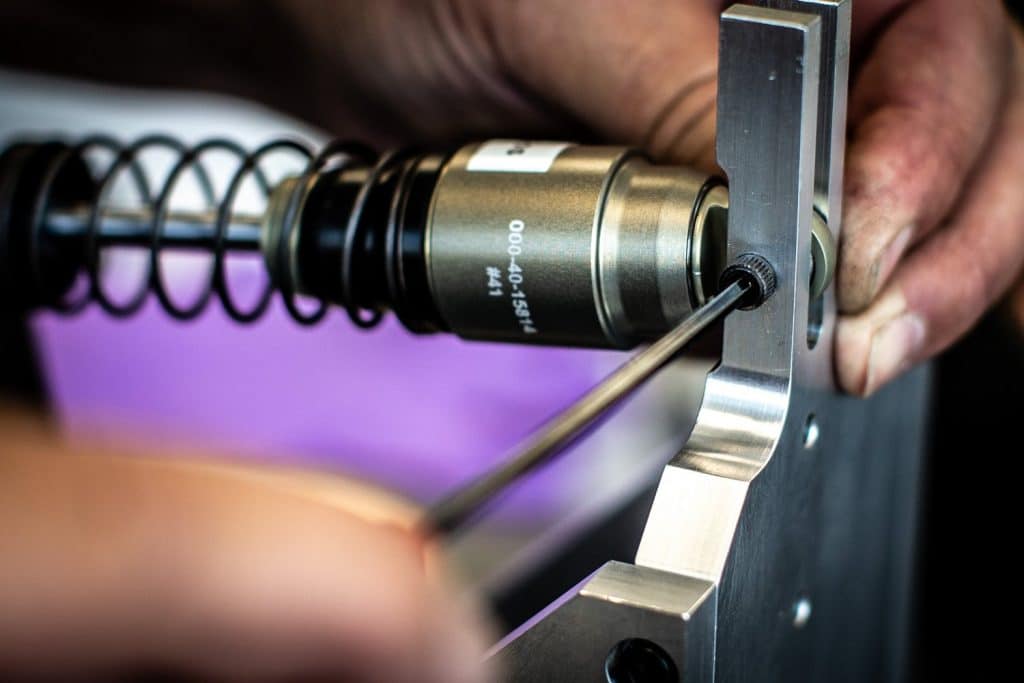
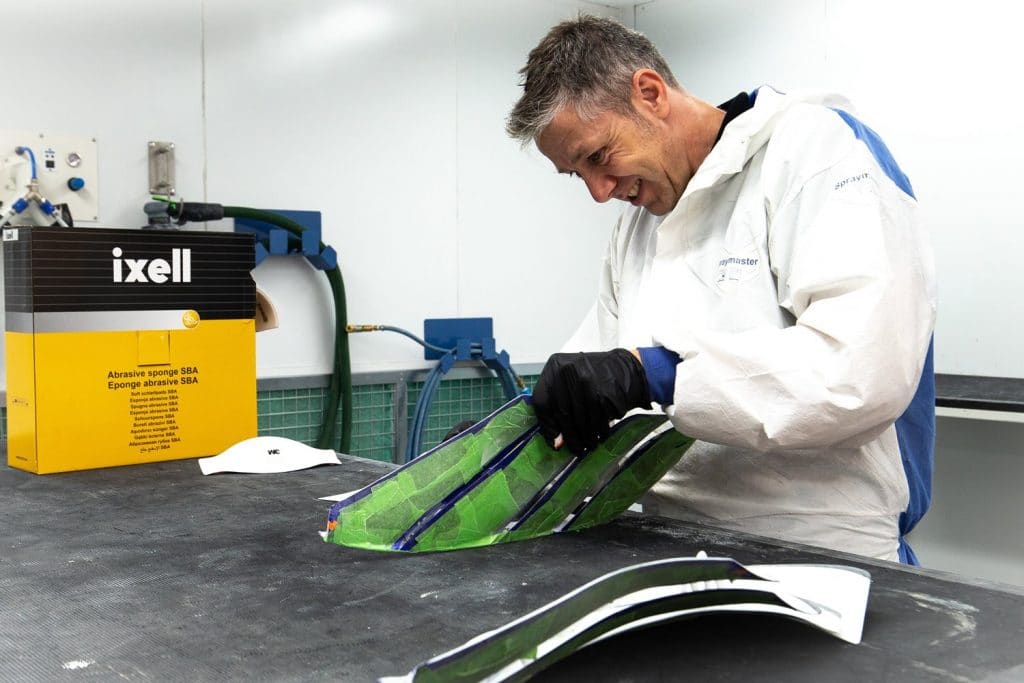
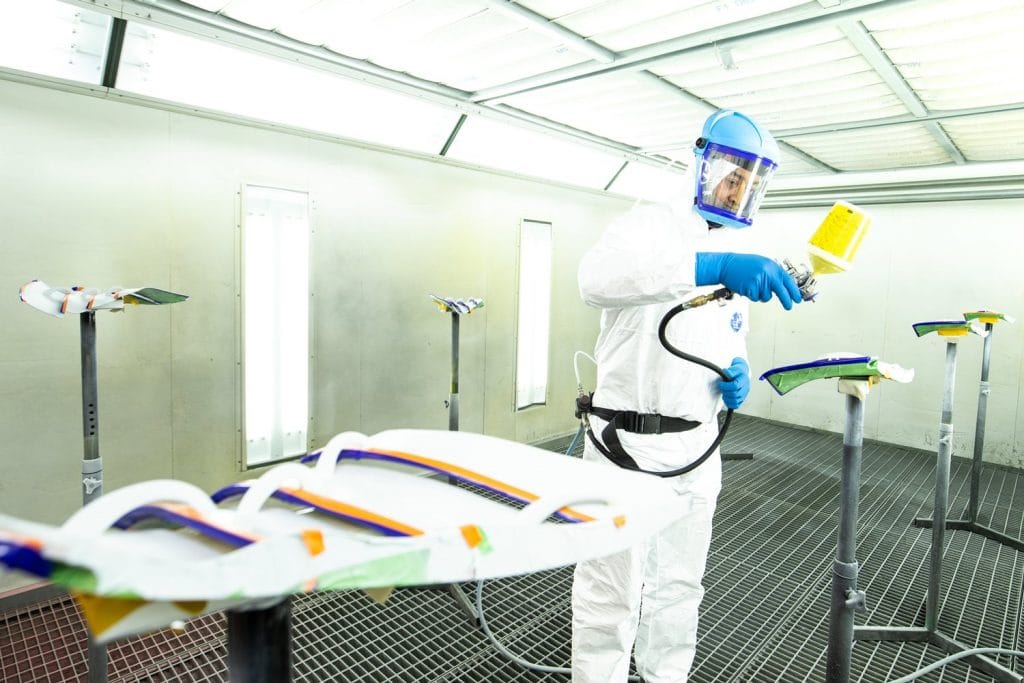
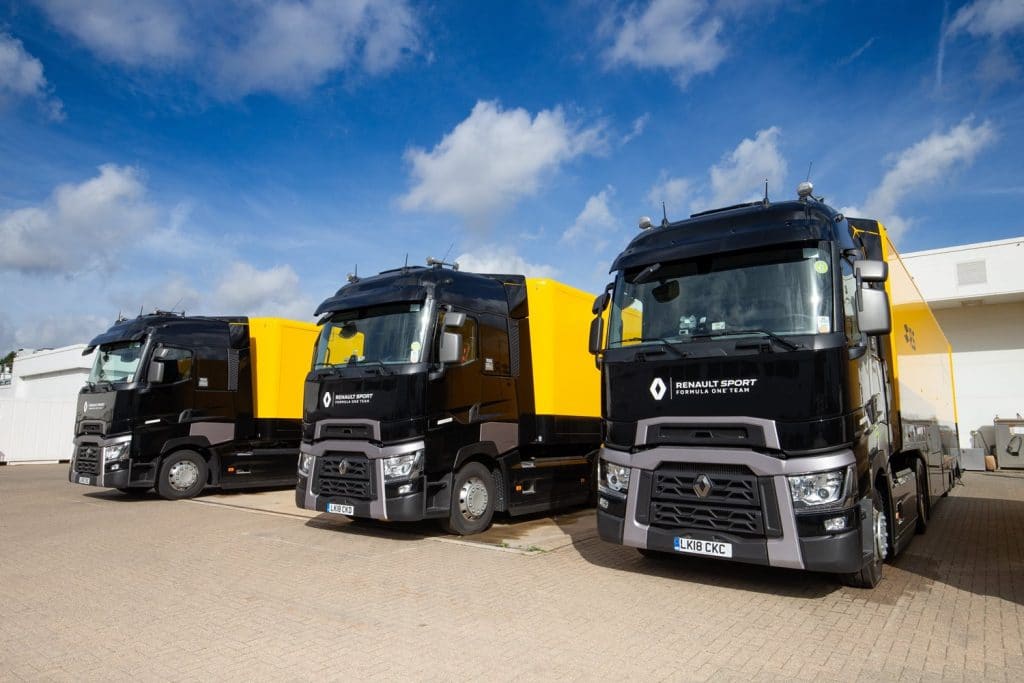
102 millions de statistiques, 50 milliards de points de données par voiture et par course
Chaque année, ce sont 102 millions de statistiques avec 50 milliards de points de données par voiture et par course qui mènent à la simulation de 1,5 milliard de stratégies par saison et 40 000 possibilités de résultats différents par tour ! La radio dans le garage, sur le muret des stands et dans le bureau d’ingénierie de la piste est reliée à la salle des opérations d’Enstone. Cette dernière a été mise pour la première fois en service en mai 2017. Elle comprend six écrans de 75 pouces, 24 postes de travail dotés de deux moniteurs de 24 pouces et un système radio de pointe similaire à celui sur le circuit. Pendant un week-end de course, les membres du GPV, les stratèges, l’aérodynamique et les systèmes d’information sont de service pour assurer communications et prises de décisions.

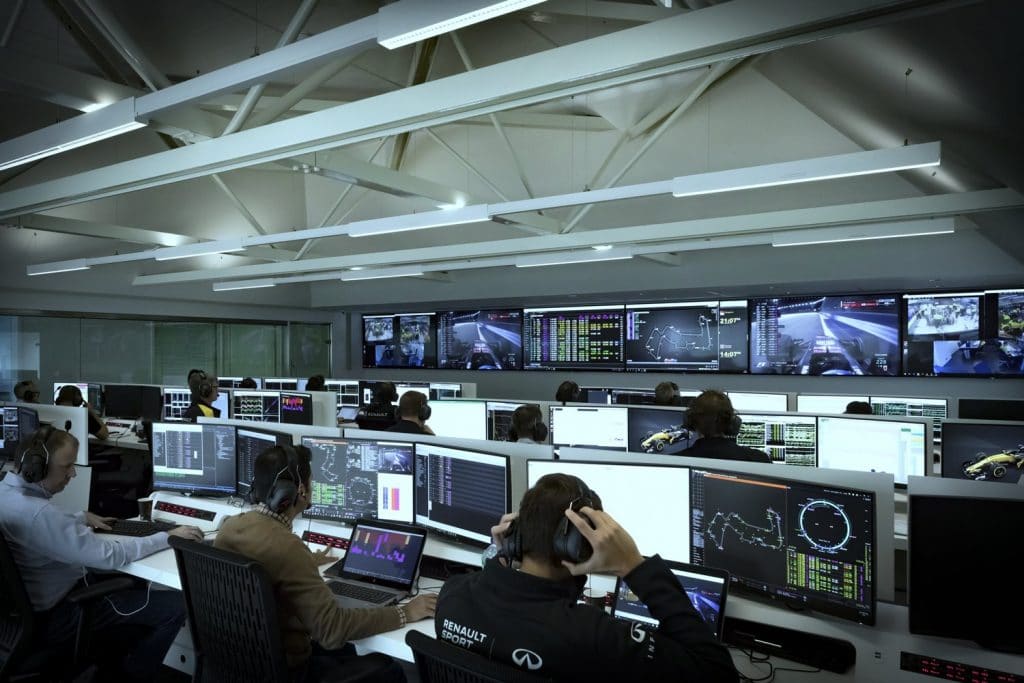
Depuis 1977, soit 40 ans en 2018, Renault Sport F1 a su transformer tous ses efforts et investissements en victoires : 12 titres constructeurs, 11 titre pilotes, 174 Grand-Prix gagnés, 251 pôle positions, 50 fois 1er et 2ème, 15 fois 1er-2ème-3ème. Avec un budget légèrement supérieur à 300 M€ par an, l’équipe française espère rejoindre le top 3 des écuries actuelles de Formule 1, pour enfin renouer avec la victoire et le titre suprême. A mi-parcours, l’écurie vise la 4ème place cette année et n’a pas le choix, Carlos Ghosn, CEO de l’Alliance Renault-Nissan-Mitsubishi, ayant dicté la règle suivante : “Nous ne sommes pas là pour participer, nous sommes là pour atteindre le plus haut niveau et gagner.”
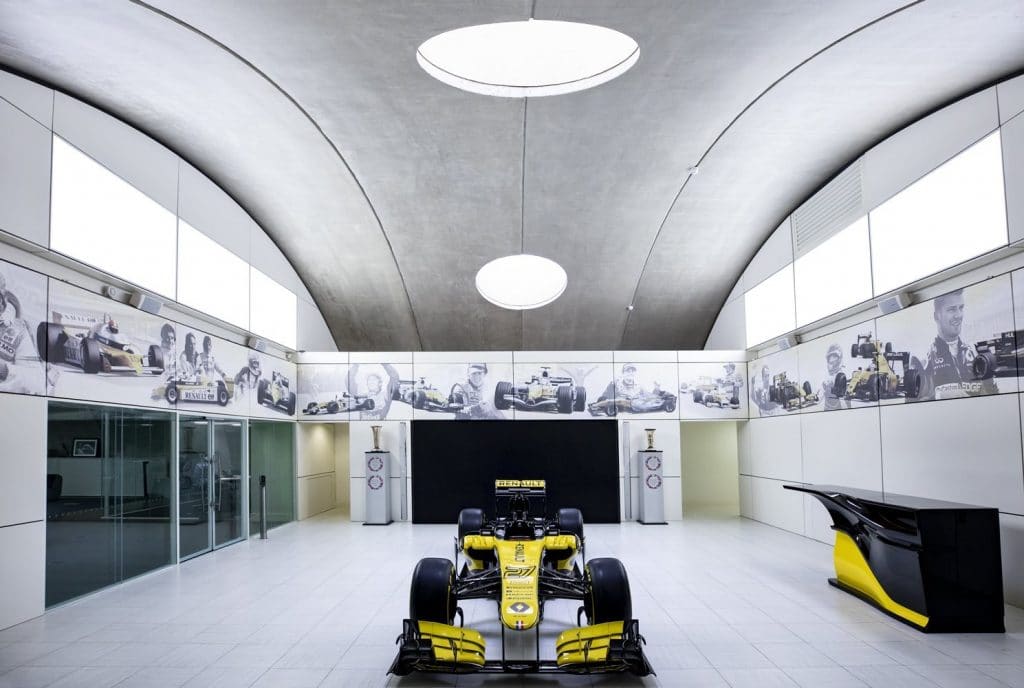
Source et crédit photos @ Renault Sport F1